Aluminum Applications in the Automotive Industry
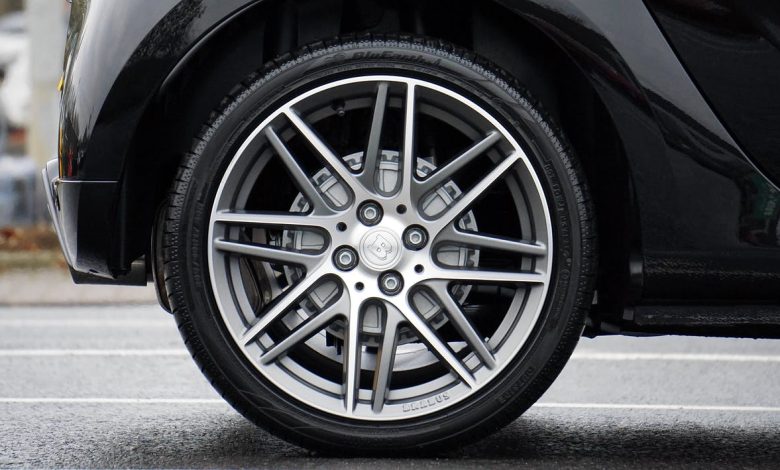
Being a versatile material, aluminum has become a widely used medium for the manufacturing of various vehicles. It is rapidly becoming a material central to the automotive industry and has been deemed to be the fastest-growing automotive manufacturing material. And given that automotive is one of the common industries for aluminum applications, it is certain that demand for this material in the industry will continue to thrive over the years.
Technological developments that improve performance metrics are inextricably linked to base material characteristics. Aluminum is actually a base metal with numerous benefits. It is a versatile material that may be alloyed with a variety of elements to improve certain mechanical features including electrical conductivity, formability, and impact resistance. However, aluminum’s excellent strength-to-weight ratio is a significant benefit in the automotive industry. And because of aluminum’s strength and durability, it meets the expectations placed on the industry to reach sustainability goals without sacrificing safety or performance. It is critical that electric automobiles compete with gas-powered vehicles in terms of performance while meeting or exceeding the same safety criteria.
Second Most Utilized Material in the Automotive Industry
The affinity for alloy bonding has led to new advances in alloys suited to the needs of the auto industry, further enhancing its lightweight nature. This made it the reason why it has been deemed to be the second most often utilized material in the vehicle industry, after steel. In the production process, 1 kg of aluminum is thought to be able to replace up to 2 kg of steel or cast iron. Moreover, it is a non-magnetic metal that effectively transmits heat and electricity. Thus, for these qualities, a wide range of aluminum applications have been innovated and developed.
A few of these applications in the said industry would include car frames and bodies, electrical wiring, wheels, lights, paint, transmission, air conditioner condenser, and aluminum pipes, engine components such as pistons, radiator, cylinder head, and magnets for speedometers, tachometers, and airbags. More will be explained further in this article. Keep on reading.
Body Panels
Body panels are the components that make up the car’s shell or outside covering. These panels give the car its overall contour while also providing protection for the engine and its interior. And while aluminum has long been used to build various car components, it has recently gained popularity. For pickup trucks, sedans, SUVs, and other vehicles, reputable automakers have experimented with constructing light, yet exceptionally robust aluminum bodywork.
Actually, one of the main advantages of aluminum as a material for automobiles would be the added fuel economy that it provides. Also, as it is a third the weight of steel, it allows for less wind resistance and a lighter overall body for the driver. This implies fewer trips to service facilities only to top off on the gas, resulting in cost savings. The reduced drag lets the driver get the most out of their car’s fuel economy and take advantage of other performance characteristics.
Wheels
One component of automobile manufacturing focuses on producing high-performance vehicles that are both affordable and safe. Heavier vehicles typically have a number of drawbacks, including inferior headlight projection, decreased fuel efficiency, and diminished steering, acceleration, and cornering capability. To address these issues, automakers are looking into the advantages of employing aluminum parts for the car body and wheels to reduce vehicle weight.
Aluminum wheels are significantly more corrosion and rust-resistant than wheels made of steel. This lowers the owner’s overall cost of ownership over time. They will not only have to pay for wheel damage repairs and replacements. But they will also profit from a car part that requires less maintenance-Articlewine.
Another advantage of using aluminum for wheel manufacturing is its strength and versatility. Alloying elements are added to aluminum alloys to improve durability, impact resistance, stress resistance, and other properties. Over time, the wear and tear on the wheels and rims decrease. This leaves the car owner with fewer scratches and scrapes to cope with.
Chassis Enclosures
Strength, fatigue resistance, and weldability are required for more complicated parts and crucial vehicle components. And another part of aluminum applications in the automotive industry lies in a car’s chassis enclosures. The entire performance of a vehicle is determined by the chassis enclosure. This serves as the car’s foundation in numerous ways. The complete chassis foundation sits atop and supports everything on the inside and exterior. From sound systems, shift sticks, gears, wheels, dashboard panels, and brake pads. Simply put, without a chassis that provides full vehicle support, it’s difficult to provide a safe and enjoyable ride.
Several advantages of aluminum chassis castings over steel chassis castings are evident in this application. Extrusions and die-cast aluminum parts offer better axial load strength at a low weight. This is in addition to their superior machinability and ease of manufacture. This technology helps the driver to ride the vehicle more safely on various terrains at consistent speeds while avoiding potential crashes-Articlewine.
Working with an aluminum chassis is also more practicable for manufacturers than working with other metals or alloys. For one thing, aluminum fabrication can be completed in a matter of days. Short lead times enable carmakers to satisfy demand without sacrificing quality. Another factor is the ease with which metal can be shaped into various shapes. Product failures and OEM returns are reduced since fewer secondary and post-processes are required.
Radiators
The purpose of a car radiator is to control the temperature inside the vehicle as well as the engine. They accomplish this by diverting the engine’s heat towards the atmosphere. Also, by providing a lower-temperature fluid to extend the motor’s life. While early radiators were built of copper brass, contemporary versions have begun to use aluminum. Aluminum is capable of moving hot air from the engine to the atmosphere faster than copper-brass radiators-Articlewine. When it comes to protecting interiors and other sensitive engine parts, higher efficiency is better for vehicles in the long term.
Using aluminum for radiators also tends to be more environmentally friendly than the use of copper brass or steel. The material can be recycled indefinitely without even losing all the qualities of its original properties. Furthermore, this is a technique for the industry to produce a smaller carbon footprint, lessening its overall environmental impact.
Key Takeaway
There are a lot more aluminum applications in the automotive-articlewine industry, bringing value to every vehicle during its manufacturing process. And as demand for higher-performing and safer car parts grows, so will the demand for aluminum to meet these needs and requirements. The material is more cost-effective, long-lasting, corrosion-resistant, and useful. Thus, innovative ways of putting aluminum parts into automobiles will undoubtedly continue to define the futures of both industries-Articlewine.
From the exterior to the engines, the diverse spectrum of aluminum alloys matches the complicated character of automobiles. Alloys with properties such as strength, corrosion resistance, impact resistance, formability, weldability, and electrical conductivity meet the industry’s safety and performance requirements.